Institute to Capture the Promise of Composites
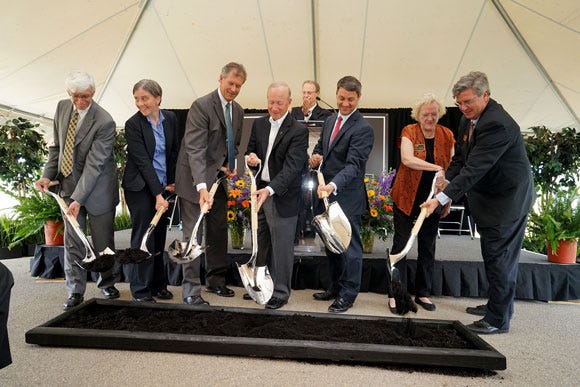
Subscriber Benefit
As a subscriber you can listen to articles at work, in the car, or while you work out. Subscribe NowComposite materials have revolutionized the aerospace industry, but their application in the automotive sector has remained elusive, mainly due to manufacturing challenges. It’s much easier to adopt new materials when building a small number of planes, but churning out hundreds of thousands of cars is a challenge that has, so far, been insurmountable on a large scale. However, Purdue University has broken ground on a $50 million institute taking aim at the auto industry and modernizing its materials.
The 62,000 square-foot Indiana Manufacturing Institute is slated to open on Purdue’s campus in mid-2016. It’s part of a $259 million U.S. Department of Energy project focused on the use of advanced composites in manufacturing.
Purdue John Bray Distinguished Professor of Engineering Dr. Byron Pipes says the aerospace industry has long since adopted the use of carbon fiber composites. These are materials that consist of carbon fibers mixed with polymers to provide lighter weight but higher strength characteristics than conventional materials. Pipes describes carbon fiber as stronger than steel, but lighter than aluminum.
Nearly half of the Boeing 787’s airframe is comprised of carbon fiber-reinforced plastic and other composites.
“The grand challenge is to convert the aerospace manufacturing technology for the automotive sector,” says Pipes. “To realize this benefit of lightweight automobiles with good crash-worthiness, we have to develop all new manufacturing methodologies and adapt them to the high-speed automotive manufacturing environment. [Each year], aircrafts are produced in the range of 1,000 to 2,000, and automobiles are produced in the range of 100,000 to 200,000.”
Pipes believes that critical volume increase implies the need for newfound speed in the manufacturing process.
“In the case of making an aircraft, we can take one or two days to make a single part,” says Pipes. “In the case of an automobile, that has to be done in three to five minutes.”
Pipes says the new institute aims to “make a lot of progress” in addressing the challenges that exist at the intersection of new materials, processes and speed. While there are innovations in materials and manufacturing processes already underway, he cautions the automotive industry is still largely a metals industry. He also notes that, as methods change, “you may need to change the machine itself that you’re using to manufacture the part.”
Institute leaders believe addressing these challenges demands collaboration with the private sector, and that’s why half of the building will be dedicated space for partnerships with Indiana companies working in composite materials. Pipes says there will be a special emphasis on small to medium-sized companies.
“We, the university, need to continue to be brought together with the problems that need to be solved,” says Pipes. “We are the tool builders, but the problem generators are the companies themselves; they know what problems need to be solved. We, perhaps, bring the latest technology to solve them.”
While these relationships are still forming, one company that has already committed to the project is Noblesville-based IDI Composites International, a “custom compounder” for molding materials.
“The growth of the marketplace is important to us. Developing new applications that promote our materials or our types of materials into different applications where they’re not currently being used—that’s one of our primary goals,” says IDI Composites Vice President Jay Merrell. “If you’re involved from the outset on a new project or program and it does, in fact, become some sort of commercial success, you have a leg up into that market space.”
Pipes believes the public-private partnership will transition technologies to the industry more rapidly. He says the automotive industry “broadly understands” that it needs to transform itself from an “all metals” operation to a multi-materials sector—generating momentum for the institute.
“We’re absolutely sure an all-metal automobile is a thing of the past,” says Pipes, an industry veteran. “I’m most excited about the convergence of the technology I know so well and have supported for so many years now finding a home in the Midwest, where automotive manufacturing will take full advantage of it.”
Pipes says Indiana could add significant value to its economy by expanding its expertise in auto production.
Pipes says major auto manufacturers are turning to composite materials to help create more efficient vehicles with lower carbon emissions.