Cummins, Oak Ridge Lab Developing Face Masks
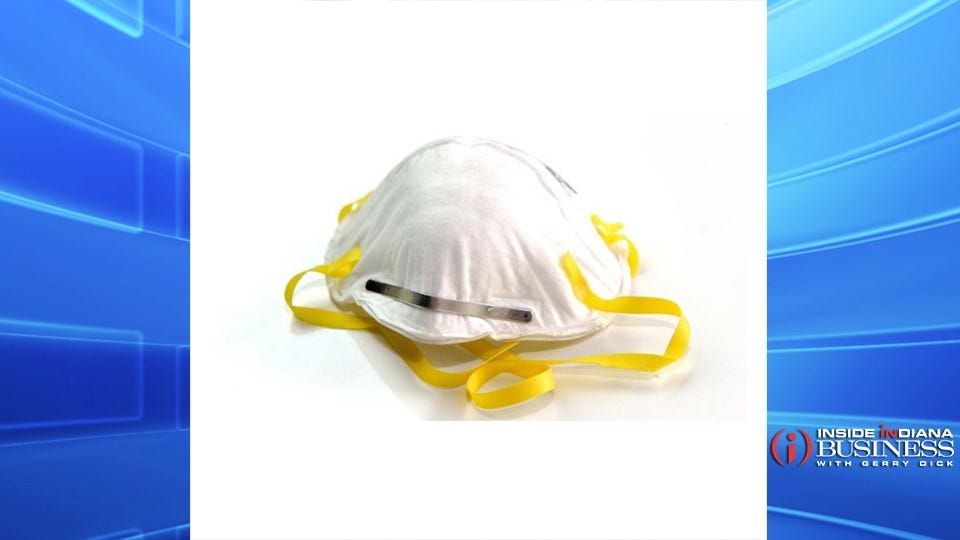
Subscriber Benefit
As a subscriber you can listen to articles at work, in the car, or while you work out. Subscribe NowColumbus-based Cummins Inc. (NYSE: CMI) and Department of Energy’s Oak Ridge National Laboratory are collaborating on a project to put more face masks and respirators in the hands of U.S. healthcare workers.
The two organizations are jointly working to produce enough filter media to supply more than a million face masks and respirators per day to U.S. healthcare facilities.
“Because of our expertise in the automotive filtration industry, we believed we could adapt to supply the filter media used in the face masks worn by healthcare providers, which are also in high demand across the nation,” said Christopher Holm, director of Filter Media Technology & IP at Cummins.
At the same time, ORNL was searching for ways to scale up production of face masks with equipment used to mass-produce precursor material for carbon fiber production at its Carbon Fiber Technology Facility.
The national laboratory said a research team had been working with the inventor of N95 filter media to improve the process.. The plan is to electrostatically charge polypropylene, creating millions of microfibers, that can be produced into sheets of fibrous material for filters.
The result is a filter than removes at least 95% of submicron particles and viruses, the benchmark needed for masks in a healthcare setting.
“We reached our target goal in only a few weeks on pilot scale melt blowing capability at the CFTF and had the capability to produce filter media for 9,000 masks per hour when we connected with Cummins for potential technology transfer and scale-up,” said ORNL’s Merlin Theodore, director of the CFTF. “Cummins was an ideal partner to scale what we had accomplished and helped us produce material that passed all required testing for filter media.”
Cummins, a powertrain and engine maker, said just two months ago, it had never produced filter media for face masks. But now, it has shipped material to multiple customers across the country for the production of millions of masks.
“We’re now looking for opportunities to expand the scope and performance of the materials we’re making, so we can serve even broader needs in the future,” said Holm.